Just-in-Time Manufacturing Implementation Guide: Reduce Inventory Costs by 40% While Boosting Efficiency
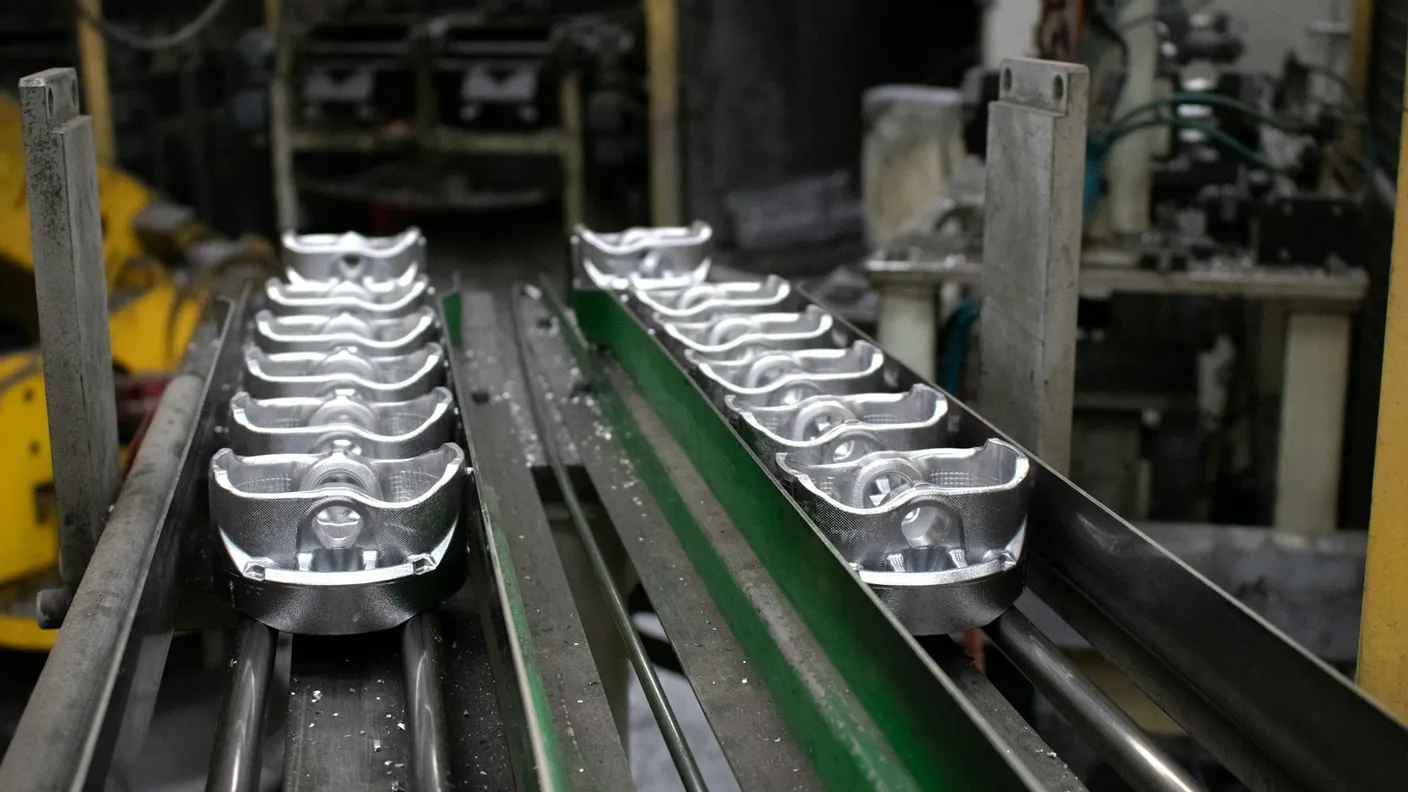
Introduction
Just-in-Time (JIT) manufacturing stands as one of the most influential production philosophies of the modern industrial era. At its core, JIT is a methodology that aims to produce only what is needed, when it’s needed, and in the exact quantity required—no more, no less.
Originating in post-World War II Japan within the Toyota Production System, JIT has evolved from a necessity-driven innovation into a global standard for manufacturing excellence. Toyota’s original implementation reduced inventory levels by 75% while simultaneously improving quality and reducing production lead times by 50%.
In today’s fast-paced manufacturing landscape, JIT remains more relevant than ever as consumers demand customization, quality, and quick delivery, while businesses face pressure to control costs and reduce environmental impact. Manufacturing companies that successfully implement JIT typically see working capital improvements of 20-40% within the first year of implementation.
For manufacturing businesses looking to implement JIT principles, precise inventory control becomes essential. Modern inventory management systems provide the real-time visibility of materials and finished goods necessary to make JIT production feasible while maintaining operational stability.
What is Just-in-Time Manufacturing?
Just-in-Time (JIT) manufacturing is a production strategy aimed at reducing flow times within production systems and response times from suppliers and to customers. Unlike traditional manufacturing models where large inventories are maintained “just-in-case,” JIT operates on a pull system—production is initiated only when there is actual demand.
Try Controlata
- Manufacturing inventory management
- Cost calculation
- Production planning
- And much more
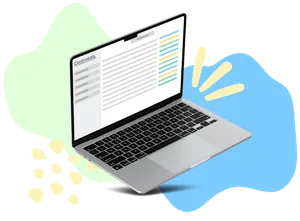
Core Principles of JIT Production
Elimination of the Seven Wastes (Muda)
- Overproduction: Producing more than immediately needed
- Waiting: Delays between production steps
- Transportation: Unnecessary movement of materials
- Over-processing: Adding features customers don’t value
- Inventory: Excess raw materials, WIP, or finished goods
- Motion: Unnecessary worker movement
- Defects: Products requiring rework or disposal
Continuous Improvement (Kaizen) Small, incremental improvements made continuously by all employees, focusing on eliminating waste and improving efficiency at every level.
Pull System Implementation Production is triggered by actual customer orders rather than forecasts, using visual signals like kanban cards to communicate production needs between workstations.
Quick Changeover (SMED) Single-Minute Exchange of Dies methodology reduces setup times from hours to minutes, enabling smaller batch sizes and greater flexibility.
Quality at the Source (Jidoka) Building quality into the process rather than inspecting afterward, with authority given to workers to stop production when defects are detected.
Technical Framework: Takt Time and Flow
Takt Time Calculation:
Takt Time = Available Production Time ÷ Customer Demand Rate
For example, if you have 480 minutes of production time per day and customer demand is 240 units, your takt time is 2 minutes per unit. This becomes the rhythm for your entire production system.
JIT vs. Traditional Manufacturing
JIT Manufacturing | Traditional Manufacturing |
---|---|
Minimal inventory (days of supply) | Substantial inventory buffers (weeks/months) |
Small production runs (hours/days) | Large production runs (weeks) |
Pull system (demand-driven) | Push system (forecast-driven) |
Quick changeovers (minutes) | Lengthy setup times (hours) |
Exposes inefficiencies immediately | Hides inefficiencies with buffers |
Continuous flow | Batch and queue |
JIT manufacturing is closely aligned with lean manufacturing principles. While lean encompasses a broader philosophy aimed at maximizing customer value while minimizing waste, JIT specifically addresses the timing and quantity aspects of production, creating the foundation for lean operations.
Core Benefits of JIT Manufacturing
When properly executed, JIT delivers measurable advantages across multiple business dimensions:
Reduced Inventory and Working Capital Requirements
JIT implementation typically reduces raw material inventory by 35-50%, work-in-progress by 70-80%, and finished goods by 60-80%. This reduction frees up valuable physical space—often 25-40% of floor space—while simultaneously releasing capital previously tied up in static inventory.
Operational Efficiency Improvements
Setup Time Reduction: SMED implementation typically reduces changeover times by 50-90%, enabling smaller batch sizes and greater product variety.
Lead Time Compression: Total production lead times often decrease by 50-75% as material waits and queue times are eliminated.
Quality Enhancement: Defect rates typically improve by 80-90% as problems are immediately visible and corrected rather than hidden in large batches.
Financial Performance Impact
Cash Flow Improvement: With inventory turns increasing from 4-6 times per year to 12-20+ times, cash conversion cycles shorten dramatically.
Space Utilization: Reduced inventory storage requirements often eliminate the need for warehouse expansion or enable facility consolidation.
Labor Productivity: Workers spend more time on value-added activities rather than handling, counting, and moving inventory.
Enhanced Production Flexibility
Demand Responsiveness: Ability to adjust production mix daily rather than weekly or monthly, enabling better customer service and reduced obsolescence risk.
Customization Capability: Smaller batch sizes make product customization economically feasible for broader customer segments.
Strengthened Supplier Relationships
JIT implementation drives development of strategic supplier partnerships focused on quality, reliability, and continuous improvement rather than simply low cost. Supplier development programs often result in mutual cost reductions and innovation acceleration.
Challenges and Limitations of JIT
Despite its advantages, JIT implementation presents significant challenges that must be carefully managed:
Supply Chain Vulnerabilities
Disruption Sensitivity: With minimal inventory buffers, any supply chain interruption can halt production within hours or days. The 2011 Japanese tsunami demonstrated this vulnerability when global automotive production stopped due to critical component shortages.
Geographic Risk: Long supply chains increase transportation delays and customs issues. Many companies implementing JIT establish regional supplier networks to reduce these risks.
Single-Source Dependencies: JIT often leads to deeper relationships with fewer suppliers, creating concentration risk if those suppliers experience problems.
Demand Variability Challenges
Forecast Accuracy Requirements: JIT works best with predictable demand patterns. Industries with seasonal fluctuations or volatile demand may need modified approaches.
Customer Behavior Impact: Unexpected order changes or cancellations can create significant disruption in JIT systems.
Implementation Complexity
Cultural Transformation: Moving from traditional batch production to continuous flow requires fundamental changes in thinking at all organizational levels.
Skill Development: Workers need training in quality techniques, problem-solving methods, and multi-skilled operations.
Management Systems: Traditional accounting and performance measurement systems often conflict with JIT principles and require modification.
Balancing Efficiency and Resilience
Strategic Inventory Placement: While JIT aims for minimal inventory, practical implementation requires careful analysis of where strategic buffers provide the best protection against disruption.
Supplier Reliability Requirements: JIT demands exceptional supplier performance—typically 99%+ on-time delivery with zero defects.
Common JIT Implementation Pitfalls and Solutions
Pitfall 1: Inadequate Supplier Development
Problem: Attempting JIT without ensuring supplier capabilities match requirements.
Solution:
- Conduct comprehensive supplier assessments covering quality systems, delivery performance, and financial stability
- Implement supplier development programs including training and process improvement support
- Establish performance metrics with regular review and improvement planning
Pitfall 2: Insufficient Demand Visibility
Problem: Implementing JIT without adequate demand forecasting and customer communication.
Solution:
- Develop collaborative planning relationships with key customers
- Implement demand sensing technologies to improve short-term forecast accuracy
- Create flexible capacity strategies to handle demand variability
Pitfall 3: Neglecting Quality Prerequisites
Problem: Reducing inventory before achieving process stability and quality control.
Solution:
- Implement statistical process control before inventory reduction
- Achieve capable processes (Cpk > 1.33) before JIT implementation
- Develop rapid problem-solving capabilities and mistake-proofing methods
Pitfall 4: Technology Integration Failures
Problem: Manual systems cannot provide the real-time visibility required for JIT operations.
Solution:
- Implement integrated inventory management systems that provide real-time material tracking
- Ensure system integration between production planning, purchasing, and inventory control
- Establish automated alerts for material shortages and quality issues
Pitfall 5: Inadequate Performance Measurement
Problem: Using traditional metrics that conflict with JIT objectives.
Solution:
- Replace efficiency-based metrics with flow-based measurements
- Implement visual management systems for real-time performance feedback
- Focus on customer service and quality metrics rather than just cost reduction
Implementing JIT Manufacturing Successfully
Successful JIT implementation requires a structured, phased approach addressing both technical processes and organizational culture:
Phase 1: Foundation Building (Months 1-3)
Process Stabilization
- Achieve statistical process control on critical operations
- Implement 5S workplace organization methodology
- Establish standard work procedures and visual management systems
Baseline Assessment
- Map current value streams to identify waste and improvement opportunities
- Measure current performance: inventory turns, lead times, quality levels, setup times
- Analyze demand patterns and variability to determine JIT feasibility
Organization Preparation
- Train management team on JIT principles and implementation methodology
- Establish cross-functional implementation teams
- Develop communication plan for organization-wide change management
Phase 2: Pilot Implementation (Months 4-8)
Select Pilot Area Choose a well-controlled production line with:
- Relatively stable demand patterns
- Cooperative workforce
- Manageable supplier base
- Measurable improvement potential
Implement Core JIT Elements
- Kanban System: Start with simple card-based pull system, sized using the formula:
Number of Kanbans = (Demand × Lead Time × Safety Factor) ÷ Container Size
- Setup Reduction: Apply SMED methodology to reduce changeover times by 50% or more
- Cellular Manufacturing: Arrange equipment in production cells to minimize material handling
Technology Implementation Deploy inventory management systems that provide:
- Real-time material tracking and consumption
- Automated reorder point calculations
- Integration with production scheduling
- Supplier communication capabilities
Phase 3: Supplier Integration (Months 6-12)
Supplier Selection and Development
- Evaluate suppliers using strict criteria for quality, delivery, and improvement capability
- Reduce supplier base to establish strategic partnerships
- Implement supplier certification programs
- Develop joint improvement initiatives
Logistics Optimization
- Establish frequent delivery schedules (daily or multiple times per day)
- Implement milk runs for multiple supplier pickups
- Consider vendor-managed inventory for critical materials
Phase 4: Expansion and Optimization (Months 9+)
Scale Successful Practices
- Expand JIT implementation to additional product lines
- Integrate sales and operations planning with JIT principles
- Develop advanced pull systems using electronic kanban
Continuous Improvement Integration
- Establish kaizen events targeting specific improvement opportunities
- Implement employee suggestion systems focused on waste elimination
- Create cross-training programs to develop workforce flexibility
JIT Success Stories in Different Industries
Automotive Industry: Toyota’s Pioneering Implementation
Toyota’s original JIT implementation in the 1950s-1970s achieved remarkable results:
- Inventory turns increased from 6 to 20+ times per year
- Manufacturing lead times reduced from weeks to days
- Quality defects decreased by over 90%
- Space requirements reduced by 50%
The Toyota Production System became the template for JIT implementation across the automotive industry, with suppliers learning JIT principles to serve Toyota and other automakers.
Electronics Manufacturing: Dell’s Build-to-Order Model
Dell revolutionized PC manufacturing by implementing JIT principles in build-to-order operations:
- Reduced finished goods inventory to less than 4 days of supply
- Achieved inventory turns of 90+ times per year
- Eliminated product obsolescence risk in fast-changing technology markets
- Enabled mass customization while maintaining cost competitiveness
Food Processing: Fresh Product Management
Food manufacturers use JIT principles to manage perishable inventory:
- Bakeries implement pull systems based on daily demand patterns
- Fresh produce processors coordinate harvesting with delivery schedules
- Dairy companies optimize routing and delivery to minimize product age
Furniture Manufacturing: Custom Production
Furniture manufacturers apply JIT to manage seasonal demand and customization:
- Reduced raw material inventory through supplier partnerships
- Implemented cellular manufacturing for product families
- Achieved make-to-order capability for custom products while maintaining competitive lead times
JIT in the Digital Age: Technology Enablers
Modern technology has transformed JIT implementation, making it more accessible and robust:
Advanced Inventory Management Systems
Modern platforms provide the real-time visibility essential for maintaining minimal inventory levels without risking stockouts. Key capabilities include:
Real-Time Material Tracking: Inventory quantities automatically update as production occurs, enabling accurate tracking at all times with immediate visibility of material consumption.
Automated Reorder Point Management: Systems calculate optimal reorder points based on lead times, demand variability, and service level targets, automatically triggering purchase requisitions when inventory reaches critical levels.
Production Integration: Direct connection between production schedules and material requirements ensures material availability aligns with production plans.
Internet of Things (IoT) and Sensors
Smart Inventory Bins: RFID and weight sensors provide automatic inventory updates without manual counting.
Production Equipment Integration: Machine sensors provide real-time production status and material consumption data.
Environmental Monitoring: Sensors track storage conditions for sensitive materials, ensuring quality maintenance in reduced inventory scenarios.
Advanced Analytics and AI
Demand Forecasting: Machine learning algorithms analyze historical patterns, seasonality, and external factors to improve demand prediction accuracy.
Optimization Algorithms: AI-powered systems optimize kanban sizing, supplier selection, and production scheduling to minimize costs while maintaining service levels.
Predictive Maintenance: Analytics prevent equipment failures that could disrupt JIT operations by predicting maintenance needs before problems occur.
Cloud-Based Integration
Cloud platforms enable seamless integration between manufacturers, suppliers, and customers:
- Real-time data sharing across the supply chain
- Collaborative planning and forecasting
- Mobile access for decision-making from anywhere
- Scalable solutions that grow with business needs
Mobile Technologies
Smartphones and tablets equipped with barcode scanning enable:
- Real-time transaction processing at point of use
- Immediate inventory updates eliminating data lag
- Worker empowerment through self-service capabilities
- Reduced administrative overhead
Financial Impact and ROI Analysis
Calculating JIT Implementation ROI
Investment Components:
- Technology systems implementation: $50,000-$500,000 depending on company size
- Training and change management: $25,000-$200,000
- Supplier development programs: $10,000-$100,000
- Process improvement initiatives: $20,000-$150,000
Typical Financial Returns (Annual):
- Inventory reduction savings: 15-25% of total inventory value
- Warehouse space savings: $5-15 per square foot eliminated
- Quality improvement savings: 2-5% of cost of goods sold
- Setup reduction productivity gains: 10-20% capacity increase
ROI Calculation Example: For a $10M revenue manufacturer with $2M inventory:
- Inventory reduction (30%): $600,000 one-time cash flow improvement
- Carrying cost savings (25% annually): $150,000 annual savings
- Quality improvements (3% COGS): $180,000 annual savings
- Implementation cost: $200,000
- First-year ROI: 265%
Working Capital Impact
JIT implementation typically improves working capital by:
- Reducing inventory investment by 25-50%
- Accelerating cash conversion cycle by 30-60 days
- Improving asset turnover ratios
- Reducing warehouse and handling costs
Hidden Costs to Consider
- Supplier development and certification expenses
- Increased transportation costs due to frequent deliveries
- Technology system ongoing maintenance and upgrades
- Additional quality assurance and inspection activities
- Risk mitigation strategies and contingency planning
Adapting JIT for Small and Medium Manufacturers
JIT principles can be successfully adapted for smaller operations with focused implementation strategies:
Start with High-Impact Areas
Material Cost Analysis: Focus initial efforts on highest-value materials that typically represent 80% of inventory investment with Pareto analysis.
Bottleneck Operations: Implement setup reduction and flow improvements at constraint operations first to maximize throughput impact.
Customer-Facing Processes: Prioritize improvements that directly impact customer delivery performance and satisfaction.
Leverage Simplified Approaches
Visual Kanban Systems: Simple card-based or bin-based pull systems require minimal technology investment while providing immediate benefits.
Supplier Partnerships: Develop close relationships with 2-3 key suppliers rather than attempting to manage large supplier networks.
Basic 5S Implementation: Workplace organization provides immediate productivity improvements and creates foundation for advanced JIT techniques.
Technology Solutions for Small Manufacturers
Cloud-based inventory management systems make sophisticated tracking capabilities accessible without extensive IT infrastructure:
- Affordability: Monthly subscription models rather than large capital investments
- Scalability: Systems that grow with business expansion
- Integration: Connect with existing accounting and planning systems
- Mobility: Access from any device for real-time decision making
Incremental Implementation Strategy
Month 1-2: Implement 5S and visual management
Month 3-4: Reduce setup times on key operations
Month 5-6: Implement simple kanban system for top materials
Month 7-8: Develop supplier partnership agreements
Month 9-12: Expand to additional product lines and materials
Measuring Success in Smaller Operations
Focus on simple, meaningful metrics:
- Inventory turns (target: doubling current performance)
- Customer on-time delivery (target: 95%+)
- Space utilization improvement
- Cash flow enhancement
- Employee engagement in improvement activities
Small manufacturers often achieve faster implementation than larger companies due to simpler decision-making processes and greater organizational agility. The key is starting with fundamentals and building systematically rather than attempting comprehensive transformation immediately.
Conclusion
Just-in-Time manufacturing has evolved significantly since its origins at Toyota, yet its core principles remain as relevant as ever in today’s dynamic manufacturing landscape. The fundamental goal—producing only what is needed, when needed, in the exact quantity needed—continues to drive efficiency improvements and competitive advantage across industries worldwide.
The benefits of properly implemented JIT are substantial and measurable: working capital improvements of 20-40%, quality enhancements exceeding 80%, lead time reductions of 50-75%, and space utilization improvements of 25-40%. These improvements translate directly to enhanced profitability and market competitiveness.
However, successful JIT implementation requires careful attention to:
- Foundation building through process stabilization and quality improvement
- Supplier development to ensure reliable, high-quality material flow
- Technology enablement for real-time visibility and control
- Cultural transformation toward continuous improvement and waste elimination
- Risk management to balance efficiency with operational resilience
Looking toward the future, JIT manufacturing continues to evolve with technological advancement:
- AI and machine learning integration for more sophisticated demand prediction and optimization
- IoT sensors providing real-time material and production visibility
- Cloud-based platforms enabling seamless supply chain collaboration
- “Resilient JIT” approaches that preserve efficiency while incorporating strategic risk mitigation
For manufacturers considering JIT implementation, the combination of proven methodologies with modern technology provides unprecedented opportunity for operational transformation. Whether leading a global enterprise or managing a small workshop, JIT principles can be adapted to specific operational contexts, delivering meaningful improvements in efficiency, quality, and customer satisfaction.
The key to success lies in thoughtful, phased implementation supported by appropriate technology infrastructure, comprehensive training, and unwavering commitment to continuous improvement. With proper planning and execution, JIT manufacturing provides a sustainable competitive advantage that grows stronger over time through ongoing refinement and optimization.
Modern inventory management systems have made JIT implementation more accessible and robust than ever before, providing the real-time visibility and control capabilities that were previously available only to the largest manufacturers. This democratization of JIT enabling technology means that businesses of all sizes can now achieve the operational excellence that was once the exclusive domain of industry giants.
The journey toward JIT excellence is not a destination but a continuous process of improvement, learning, and adaptation. Organizations that embrace this philosophy while leveraging modern technology capabilities position themselves for sustained success in an increasingly competitive global marketplace.