MRP Implementation Guide for Small Manufacturers: Step-by-Step Resource Planning
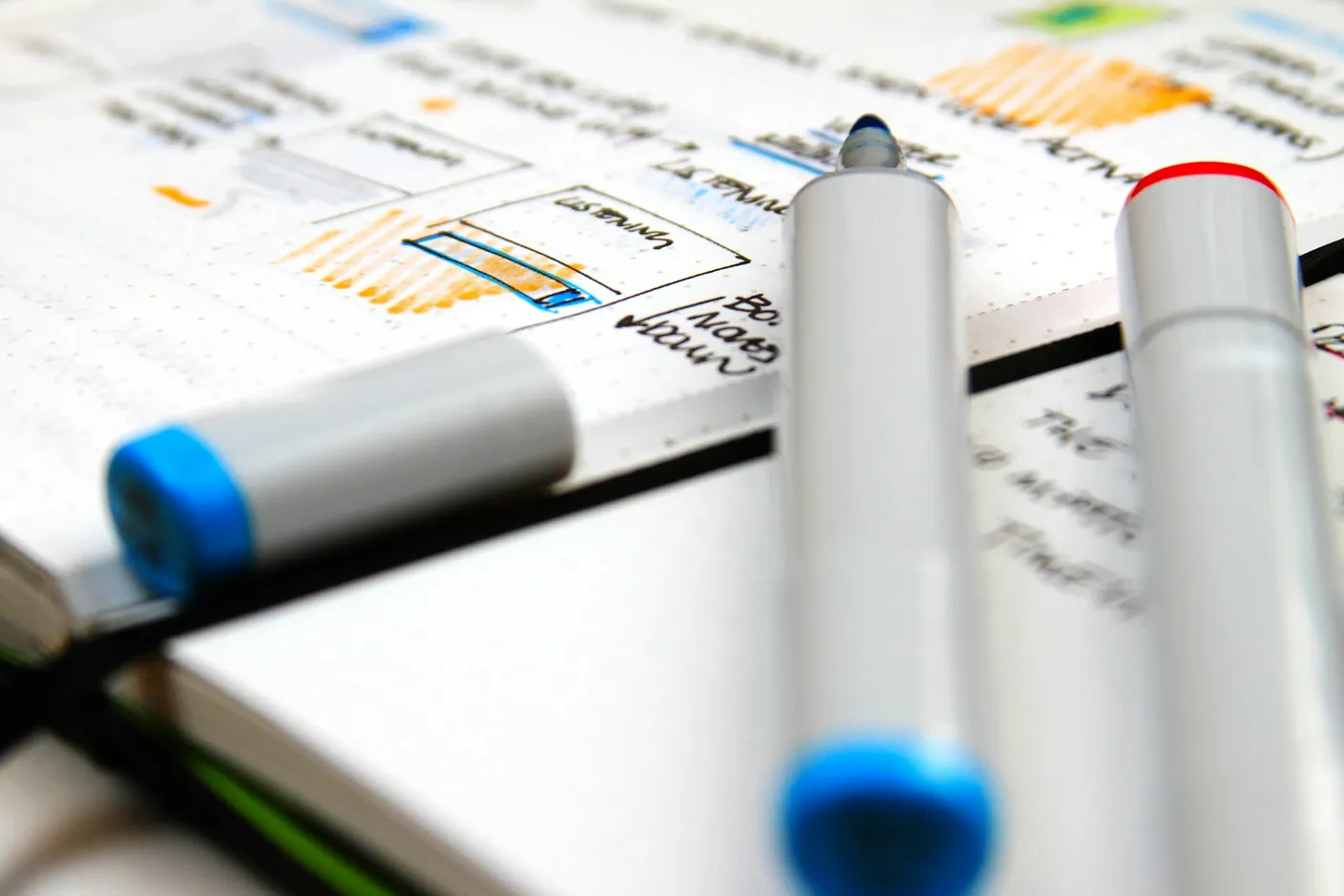
Introduction: Why Small Manufacturers Can’t Afford to Ignore Resource Planning
Manufacturing Resource Planning (MRP) fundamentally transforms how small manufacturers manage production, inventory, and resources. Unlike Enterprise Resource Planning (ERP) systems that encompass finance and HR, MRP specifically targets manufacturing operations—inventory control, production scheduling, materials planning, and cost calculation.
Most small manufacturers operate with informal systems: Excel spreadsheets tracking inventory, handwritten production schedules, and purchasing decisions based on gut instinct. These manual approaches work initially but create serious bottlenecks as operations scale beyond 10-15 employees or when managing more than 50 active products.
Common warning signs indicate when manual processes are failing. Production frequently stops due to missing materials despite believing you had adequate stock. Customer delivery promises become unreliable because you can’t accurately predict completion times. Rush orders from suppliers become routine, increasing material costs by 15-25%. Product pricing relies on rough estimates rather than actual cost data, potentially eroding margins.
The competitive landscape has fundamentally shifted. Customer expectations for shorter lead times, real-time order status, and consistent quality create pressure on manufacturers regardless of size. Small manufacturers using manual processes struggle to match the responsiveness that modern customers expect, often losing business to competitors with better operational control.
This guide addresses the specific challenges small manufacturers face when transitioning from manual processes to systematic resource planning. You’ll learn practical strategies for system selection, phased implementation approaches that minimize disruption, and measurement techniques that demonstrate clear return on investment.
Try Controlata
- Manufacturing inventory management
- Cost calculation
- Production planning
- And much more
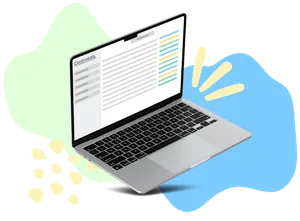
The Technology Evolution That Made MRP Accessible
Manufacturing Resource Planning emerged in the 1960s when companies like Toyota pioneered systematic production control methods. Early systems required mainframe computers, dedicated programming staff, and implementation timelines measured in years. These systems remained expensive and complex, requiring IT infrastructure that small manufacturers couldn’t justify.
Cloud computing fundamentally changed this accessibility equation. Modern MRP systems operate entirely through web browsers, eliminating server hardware requirements. Software-as-a-Service (SaaS) pricing models replaced large license fees with monthly subscriptions that scale with business growth.
Mobile technology enables real-time data access from production floors, eliminating paper-based delays. Production staff can update order status immediately, inventory levels adjust automatically as materials are consumed, and managers can monitor operations remotely.
The critical distinction for small manufacturers lies in system design philosophy. Enterprise MRP assumes complex organizational hierarchies and extensive customization. Small-manufacturer solutions like Controlata prioritize rapid implementation, intuitive operation, and core functionality that delivers immediate value without requiring process redesign.
Core MRP Components That Transform Manufacturing Operations
Effective MRP systems integrate multiple components that eliminate inefficiencies common in manually managed operations. Understanding these components helps prioritize implementation phases and evaluate system capabilities.
Real-Time Inventory Management with Automated Tracking
Modern inventory management provides comprehensive visibility across your entire operation. Systems track materials through multiple states: raw materials in storage, work-in-progress items at manufacturing stages, finished goods awaiting shipment, and reserved inventory allocated to specific orders.
Real-time tracking includes automatic inventory updates as materials move through production, barcode scanning integration for rapid receiving and picking, lot and batch tracking for quality control, and automated low-stock alerts based on consumption patterns and supplier lead times.
Digital Bill of Materials Management
Bills of Materials serve as the foundation for accurate production planning and cost calculation. Digital BOM management creates dynamic blueprints connecting materials to products while supporting complexity typical in custom manufacturing.
Effective BOM structures accommodate multi-level products with sub-assemblies, alternate component specifications when materials become unavailable, and revision control that maintains historical versions. BOM costing automatically calculates material costs based on current pricing and rolls up labor and overhead costs.
Production Planning That Balances Demand with Capacity
Production planning transforms customer orders into executable manufacturing schedules considering available capacity, material availability, and delivery requirements. Finite capacity scheduling respects realistic production limitations while work center definitions reflect actual equipment capabilities.
Visual scheduling tools make production plans easily understandable across your organization. Gantt charts and dashboard displays help communication between management, production staff, and customer service while identifying potential conflicts before they impact delivery performance.
Integrated Procurement and Cost Calculation
Automated procurement eliminates reactive purchasing that disrupts manufacturing operations. Systems generate purchase requirements based on production plans, current inventory levels, and established reorder points, shifting from reactive to proactive material management.
Comprehensive cost calculation encompasses material costs, labor time, overhead allocation, and indirect expenses. This information enables informed pricing decisions and identifies profitability improvement opportunities that might otherwise remain hidden.
Implementation Challenges Specific to Small Manufacturers
Small manufacturers face unique obstacles when implementing MRP systems that differ from challenges faced by larger organizations. Understanding these potential pitfalls enables better preparation and realistic implementation planning.
Resource Constraints and Competing Priorities
Small manufacturers typically operate with minimal administrative overhead, where individuals handle multiple responsibilities. The person managing inventory may also handle purchasing, customer service, and quality control. This makes dedicating sufficient time to system implementation challenging without disrupting revenue-generating operations.
Budget constraints often force difficult timing decisions between immediate operational needs and longer-term improvements. When equipment requires unexpected repair or customers place rush orders, MRP implementation may be postponed unless dedicated resources and timelines are established beforehand.
Change Management in Established Teams
Small manufacturing teams often develop strong informal communication patterns that feel efficient despite lacking systematic approaches. Long-term employees may have invested significant effort developing expertise with manual systems and view new technology as invalidating this investment.
Resistance often stems from legitimate concerns about job security rather than simple opposition to change. Experienced employees may worry that systemizing their knowledge reduces their value or creates vulnerability during economic downturns.
Data Quality Issues and Integration Complexity
Many small manufacturers discover significant data quality problems when preparing for MRP implementation. Inventory records may be incomplete, Bills of Materials might exist only in workers’ knowledge, and historical usage patterns may not be documented systematically.
Small manufacturers frequently use accounting software, e-commerce platforms, or specialized tools that must integrate with new MRP systems. Ensuring proper data flow between systems requires careful planning and often technical configuration beyond basic setup.
Step-by-Step Implementation Strategy
Successfully implementing MRP requires a systematic approach that minimizes operational disruption while building confidence through measurable improvements.
Phase 1: Assessment and Foundation (Weeks 1-8)
Begin with comprehensive operational assessment documenting current processes and identifying improvement priorities. Map workflows by following materials from receipt through production to shipment. Document how information flows between areas and identify points where delays or errors commonly occur.
Establish baseline metrics for key performance indicators including inventory turns (annual cost of goods sold divided by average inventory value), on-time delivery performance, and time spent on manual processes like inventory checking and production scheduling.
Complete initial system setup focusing on core configuration rather than replicating every aspect of current operations. Enter basic company information, define primary storage locations, and establish key product categories using standard configurations. Create user accounts and establish security roles providing appropriate access levels.
Phase 2: Inventory Management Implementation (Weeks 9-16)
Start active system use with inventory management, as accurate stock information provides the foundation for all other MRP functions. Conduct focused physical inventory count for key materials to establish accurate starting quantities.
Input current inventory data starting with highest-value and most frequently used materials. Establish location assignments and implement standardized receiving procedures that update inventory levels immediately when materials arrive.
Configure low-stock alerts based on actual consumption patterns and supplier lead times. Implement regular cycle counting procedures to maintain accuracy over time, focusing initially on high-value and fast-moving items.
Phase 3: Production Planning and BOMs (Weeks 17-24)
Begin developing digital Bills of Materials for key products, starting with highest-volume items. Work closely with production personnel to ensure BOMs reflect actual manufacturing processes rather than theoretical designs.
Implement production order creation and tracking for actual manufacturing runs. Train production personnel to update order status as work progresses, providing visibility into work-in-progress and enabling accurate delivery estimates.
Define work centers reflecting actual production capabilities and establish realistic capacity constraints. Begin basic production scheduling by creating work orders based on customer requirements and material availability.
Phase 4: Procurement and Optimization (Weeks 25-32)
Establish reorder points and preferred suppliers for key materials based on consumption patterns observed during earlier phases. Configure the system to generate purchase requirements automatically when materials fall below defined minimums.
Begin using cost calculation features to understand true product costs including materials, labor, and overhead. Implement standard reports for key performance indicators and begin using system data for trend analysis and performance monitoring.
Complete integration with existing business systems including accounting software and e-commerce platforms. Conduct comprehensive review of implemented processes and identify refinement opportunities based on actual usage experience.
Essential Features for Small-Manufacturer Success
When evaluating MRP solutions, specific features determine whether implementation succeeds or becomes an expensive distraction.
Cloud-Based Architecture and Mobile Access
Cloud deployment eliminates expensive on-premises hardware while providing enterprise-level security. Automatic software updates ensure access to latest features without interrupting operations or requiring technical intervention. Mobile compatibility enables real-time updates from production floors and remote locations.
Intuitive Interface Design
User interface design significantly impacts adoption success where extensive training resources aren’t available. Effective interfaces use familiar design patterns and logical navigation enabling rapid learning. Visual workflow design should mirror actual operational processes rather than requiring adaptation to arbitrary software logic.
Flexible Pricing and Integration Capabilities
Subscription-based pricing aligns system costs with business growth while avoiding large upfront investments. Multiple pricing tiers should accommodate different business sizes without forcing payment for unnecessary features.
Comprehensive integration capabilities prevent duplicate data entry while ensuring consistency across business functions. API availability provides flexibility for custom integrations with specialized tools or unique requirements.
Comprehensive Support and Built-in Reporting
Small manufacturers typically lack dedicated IT support, making vendor support quality critically important. Multiple support channels and implementation guidance about best practices prove essential for success.
Built-in reporting features should provide standard reports for common needs like inventory valuation and production performance. Visual dashboards highlight key indicators while exception reports focus attention on items requiring immediate action.
Controlata exemplifies these essential features with a platform specifically engineered for small manufacturers, balancing sophisticated planning capabilities with operational simplicity.
Measuring ROI and Operational Improvements
Implementing appropriate MRP systems delivers measurable returns, but benefits must be tracked systematically to validate investment and identify improvement opportunities.
Inventory Optimization Results
Track inventory turnover rates by calculating annual cost of goods sold divided by average inventory value. Many small manufacturers achieve inventory turn improvements of 30-60% within the first year as better planning reduces both overstock and emergency purchasing.
Monitor inventory accuracy by comparing system records to physical counts during cycle counting. Most manufacturers achieve 95%+ inventory accuracy within six months compared to 70-85% with manual systems. Track stockout frequency, with effective systems reducing stockouts by 60-80% through better planning.
Production Efficiency Gains
Measure Overall Equipment Effectiveness (OEE) by tracking availability, performance, and quality factors. Many small manufacturers see 15-25% OEE improvements through better scheduling and reduced material-related downtime.
Track production cycle times from order receipt to completion. Improved planning typically reduces cycle times by 20-40%, enabling faster customer response and potentially allowing premium pricing for quick delivery.
Customer Service Enhancement
Monitor on-time delivery rates, which typically improve to 90%+ after effective MRP implementation compared to 70-80% with manual planning. Track quote accuracy and response time, with many manufacturers reducing quote preparation time by 50% while improving accuracy.
Cost Accuracy and Profitability
Compare estimated product costs before implementation to actual costs calculated through the MRP system. Better cost visibility enables informed pricing decisions while identifying improvement opportunities previously hidden by poor cost visibility.
Track administrative time savings from automated processes including inventory checking, purchase order generation, and production scheduling. Many manufacturers reduce administrative time by 40-60% through automation.
Most small manufacturers using appropriately scaled MRP systems achieve full payback within 8-18 months of complete implementation, with consistent measurement validating success while identifying continued improvement opportunities.
Conclusion: Building Your Foundation for Manufacturing Excellence
Manufacturing Resource Planning represents a transformative investment for small manufacturers seeking competitive advantage in today’s demanding marketplace. The evidence is compelling: manufacturers implementing appropriate MRP systems consistently achieve 30-60% improvements in inventory turnover, 20-40% reductions in production cycle times, and 90%+ on-time delivery performance.
Modern MRP solutions have eliminated traditional barriers through cloud-based deployment, intuitive interfaces, and flexible pricing models that align costs with business growth rather than requiring substantial upfront investments. The phased implementation strategy outlined enables systematic progress while building confidence through early wins.
System selection proves critical for success. Enterprise-focused MRP systems typically fail in small manufacturing environments due to complexity and cost. Solutions like Controlata specifically address small manufacturer needs through simplified interfaces, rapid deployment, and supportive pricing models.
The competitive landscape continues evolving in ways that favor manufacturers with systematic operational control. Customer expectations for shorter lead times and consistent quality create pressure regardless of company size. Small manufacturers using manual processes increasingly struggle to match the responsiveness that modern customers expect.
Implementation success requires commitment beyond initial system deployment. Organizations achieving sustained benefits view MRP implementation as the beginning of a continuous improvement journey rather than a one-time project. Regular performance monitoring and process optimization ensure continued value while adapting to evolving business requirements.
Begin your MRP journey by conducting honest assessment of current operational challenges and identifying specific improvements that would have greatest impact on business performance. Whether struggling with inventory accuracy, production delays, or cost visibility, modern MRP solutions provide practical tools to address these challenges systematically.
Ready to transform your manufacturing operation through strategic resource planning? Start by evaluating your current pain points and discovering how accessible solutions like Controlata can address them effectively while building a foundation for operational excellence that supports sustainable business growth.