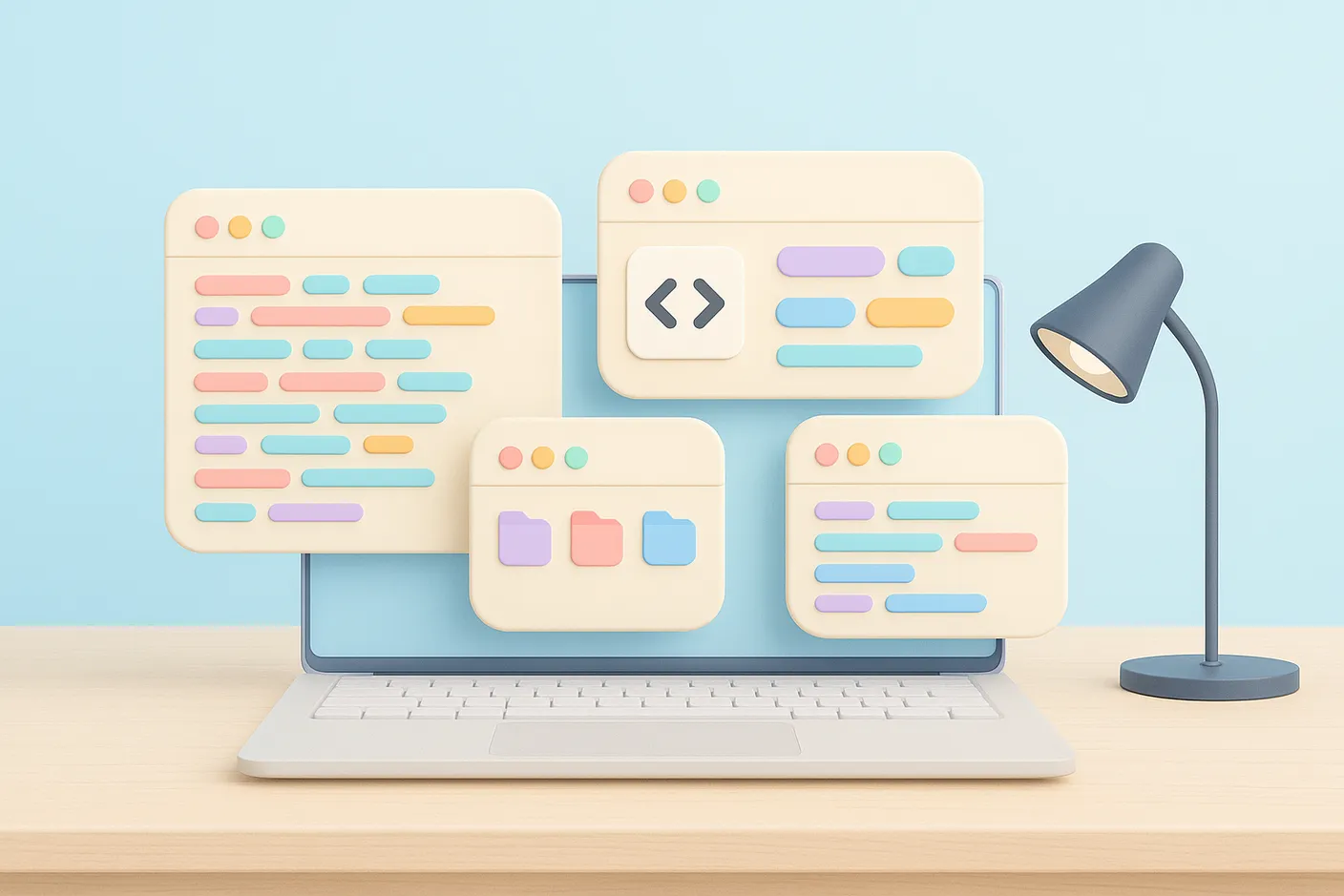
May has been an incredibly productive month for Controlata development! We’ve shipped 8 significant updates that will make your experience with the system even more efficient and user-friendly. Here’s a detailed breakdown of each new feature.
Column Customization
You can now customize column display on any screen in Controlata to fit your specific needs. Don’t use certain fields? Hide them! Need additional information? Add the missing columns.
Column settings can be saved either for yourself personally or for all users in your company.
Planned Stock Changes
Material and product cards now display planned stock changes. The system shows how stock levels will change based on all scheduled operations: supplier deliveries, production plans, and customer orders.
Click on the planned quantity to see a detailed breakdown: how much material will arrive from suppliers, how much will go into production, and how much finished product will be shipped to customers. This information can also be displayed in the main list through column customization.
Stock Levels Across All Storage Locations
In material or product cards, you can now quickly view stock levels across all storage locations. Simply click on the warehouse name to see inventory distribution across all your locations.
Enhanced History
Transaction history in material, product, and resource cards now includes not only completed operations but also planned ones. We’ve added convenient filters: you can view only actual transactions, only planned ones, or everything together.
Flexible Inventory Audits
Previously, inventory audits could only be created with the current date. Now you can specify any audit date — this is especially important if you conducted the count yesterday but are entering the data today. We’ve also added the ability to delete inventory audits if they were created by mistake.
Production Batch Size
You can now specify a production batch size for each product. This is the quantity for which all materials and resources in the bill of materials are calculated.
To set batch size, enable this option in settings.
Example: You run a bakery and produce bread loaves. Your bill of materials specifies 10 kg flour, 6 L water, and 200 g yeast. If you set the batch size to “100 pieces,” the system will understand that these ingredient quantities are needed to bake 100 loaves. When planning production of 500 loaves, the system will automatically recalculate: you’ll need 50 kg flour, 30 L water, and 1 kg yeast.
SKU Display in Transactions
A new option to display product SKUs in transactions has been added to settings. When enabled, SKUs will appear in all product transactions — production, orders, write-offs, and transfers. You’ll also be able to search for and add products not only by name but also by SKU — very convenient when you have many similar items.
SKU for Materials
Similar to products, you can now enable SKU for materials. The functionality works exactly the same way: SKUs appear in transactions and you can search by SKU.
Missing Something?
We’re all ears! If there’s a feature you need, submit your idea in our ideas portal. Ideas with strong community support have the best chance of making it onto our roadmap and into future releases.